magnustullock
New Member
Hi,
Have been using straight tracked circuit boards till now with a ton on soldered wires. However I now want to try to tidy all that up with a designed PCB. I am using design spark and have included the pickaxe libraries. I have added the 28x1 chip as well as the resistors required but the tracks are running between the pickaxe pins (will upload an image later). Can anyone confirm this is ok for a pickaxe circuit to have tracks this close? will tracks that close to pins not suffer from cross talk or electric noise? Are there any recommended settings in terms of track and pad width for design spark to make it more suitable for picaxe?
Thanks
Magnus
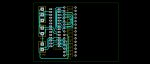
Have been using straight tracked circuit boards till now with a ton on soldered wires. However I now want to try to tidy all that up with a designed PCB. I am using design spark and have included the pickaxe libraries. I have added the 28x1 chip as well as the resistors required but the tracks are running between the pickaxe pins (will upload an image later). Can anyone confirm this is ok for a pickaxe circuit to have tracks this close? will tracks that close to pins not suffer from cross talk or electric noise? Are there any recommended settings in terms of track and pad width for design spark to make it more suitable for picaxe?
Thanks
Magnus
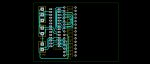
Last edited: